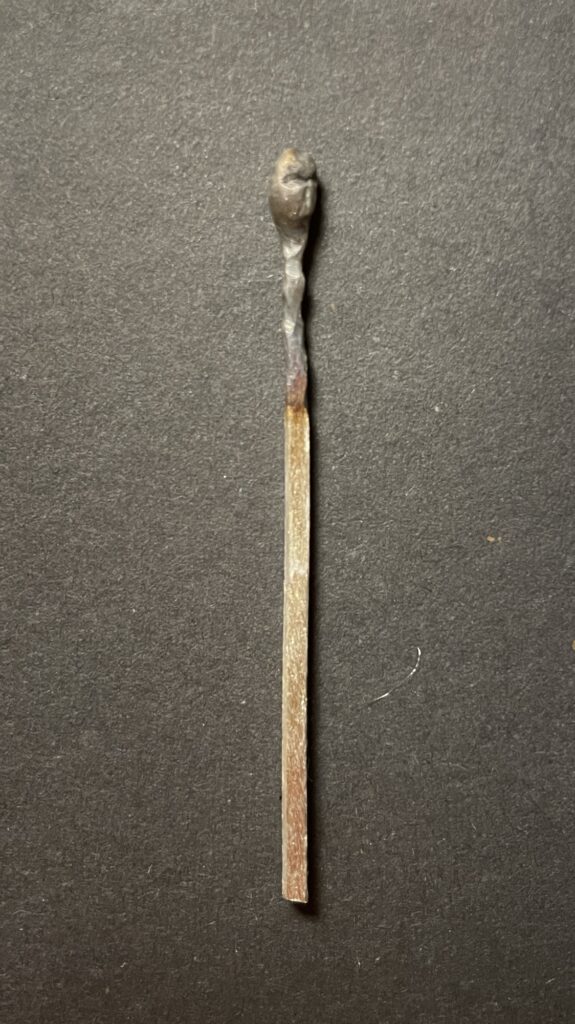
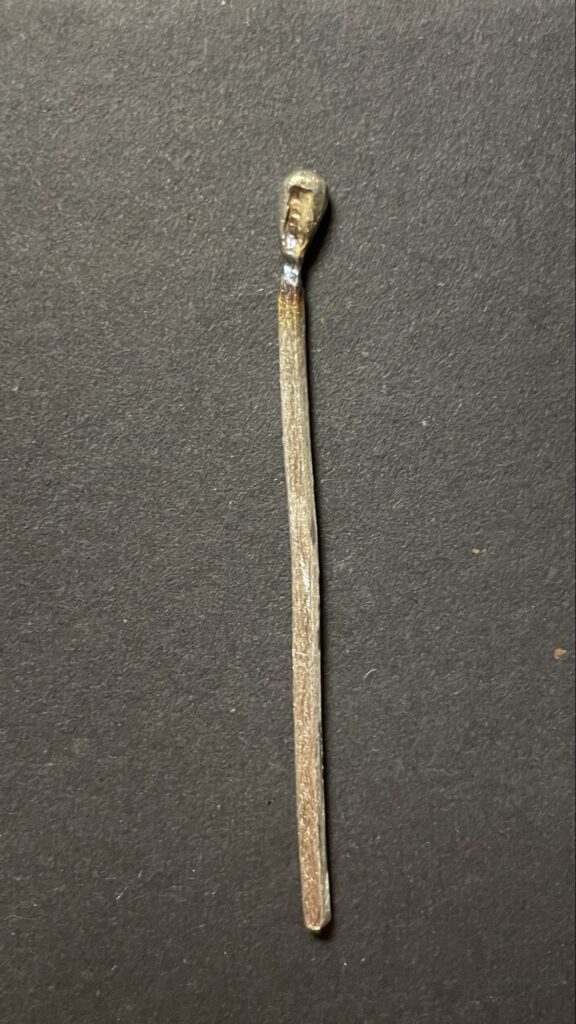
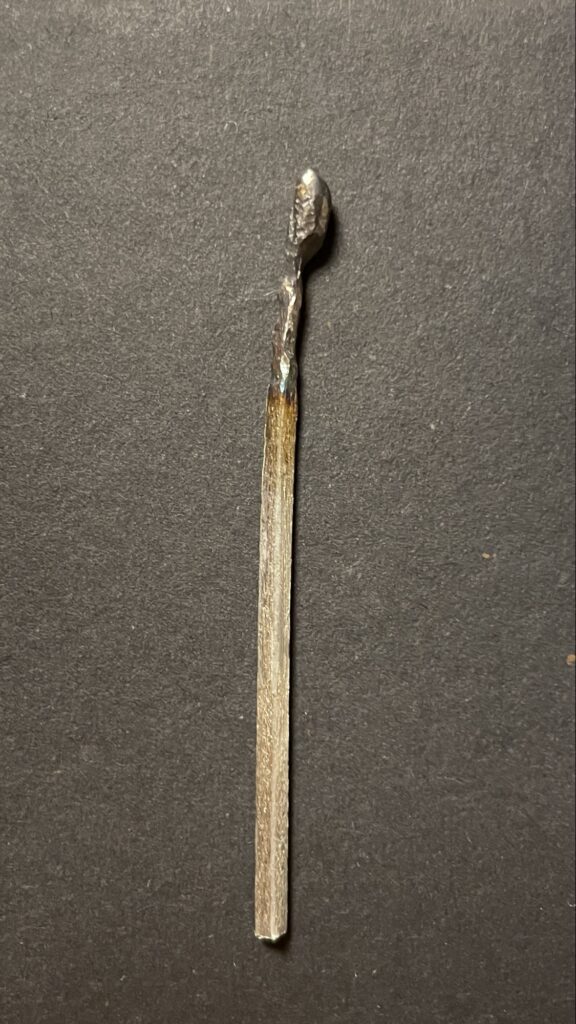
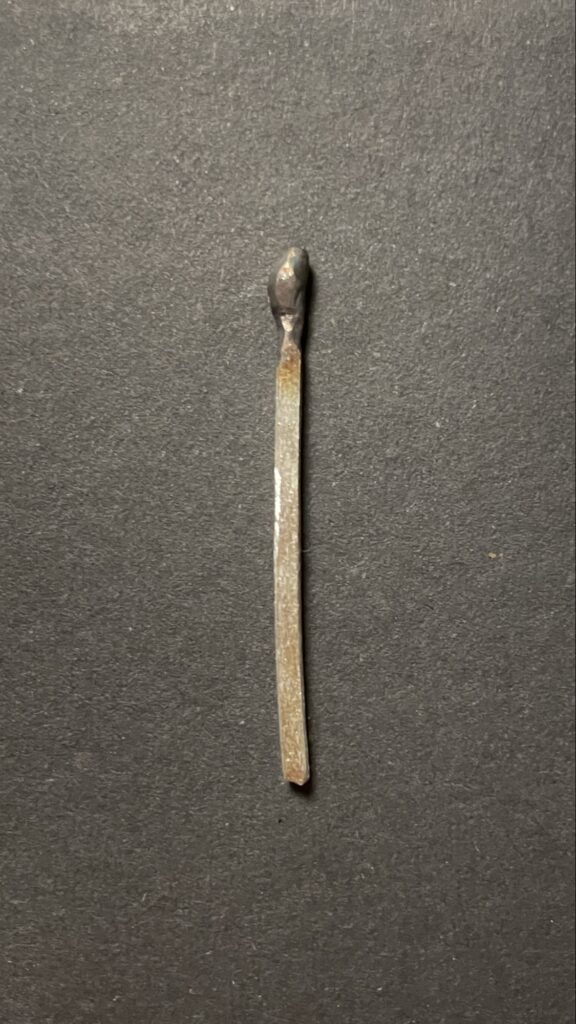
Today I worked with Anna Butwell at Metal Atelier, to make matches out of silver. I was expecting to use the sand cast method that I‘d seen on YouTube to make replicas of everyday objects to I bought my matches with me. Actually, I‘d forgotten to get matches until the last minute so I went to shops on the way. In the Mein Markt near me I asked the woman who worked their for „ich weiß nicht auf Deutsch, aber etwas um Feuer zu machen“ and mimed striking the match. A nearby shopper said „Streichholz“ and she was right, that was what I wanted. And at the counter the man gave me an option of Red or Green American Spirit matches and I wanted some more like household matches but they didn‘t have any others, so I chose Green and he said „Chen Chen“. I didn‘t say ‚Was“ but rooted around in my bumbag while I tried to decipher the two syllables. I glanced up: „Chen chen!“ he repeated. „Chen chen?“. „Ja, nicht ein euro, chen chen“. I gave him my euro coin and got ninety cents back.
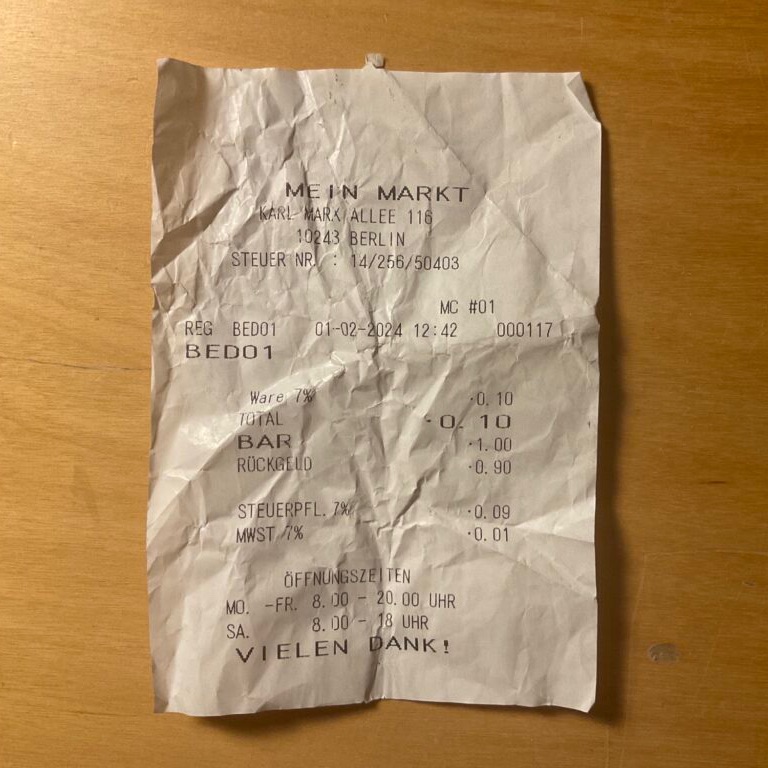
Anyway, I got some other matches too, from Edeka. But Anna had different ideas. We were going to work with silver wire. I first had to use the Spaghetti Maker to stretch, compress and narrow the wire, making sure to rotate it so the square shape didn‘t collapse into a diamond with sharp corners. In fact that did happen – I tightened the spaghetti Maker too much (more than the recommended 10-15 degrees) and I was left with flaps, which if compressed back in, would flake out again. So I had to get a file and file it away. The powder and flakes of silver that fall are put into a pot and Anna takes them back to the Jewellers Supplier to get money on her account.
While you‘re compressing, the crystalline structure of the silver collapses, and eventually it becomes harder to compress – it becomes denser. But if you apply heat, with a Bunsen burner type thing (was it propane?) keeping the hard orange bit of flame a centimetre or two from the wire and keeping going until it starts to glow, before taking it in prongs and dumping it in a glass bowl of water, then the crystalline structure refigures and you can carry on.
It curls a bit while you‘re doing this, so to get it kind of straightened out you take ‚the good hammer‘ (they‘re all good hammers, Anna backtracks, when I call it that too) and, letting gravity be your friend, you bend at the elbow and let the hammer fall on the wire.
So then there‘s the interesting bit coming up. Anna cuts the wire with the big shears which she doesn‘t let new people use because even though she is insured she thinks that that is the most dangerous piece of equipment in the place. I marked the length on the wire, measuring against the matches I‘d brought.
Then Anna has a great method for making match shapes. You clamp the pieces of wire sticking upwards in this other kind of tong, it‘s called cross locking tweezers, and then you put the flame of the burner closer to the metal this time, not only heating the tip, but focussing there, and then eventually the tip goes orange (it happens in a rush) and then flops down in a bud shape onto the metal below. Here‘s one that kind of fucked up so I didn‘t carry on shaping it (also not really enough time) but it gives a good impression of how the process works.
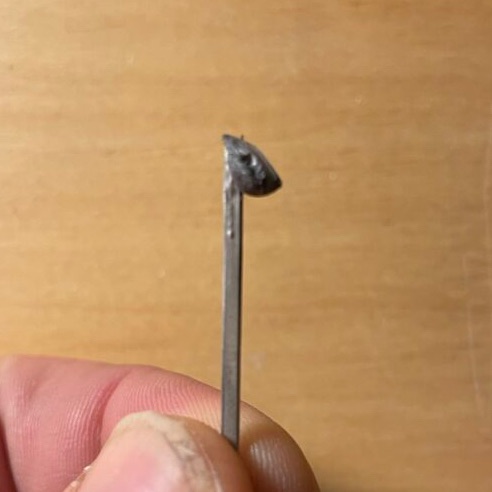
Then you dunk them in water, then into a diluted sulphuric acid bath to bring the, I don‘t really know, like, the good silver out(!) and then it‘s to the wooden desk and the vice. You get to filing, shaping with small files, flat, or curved, or with a triangular cross section. You rest the match against a wooden bench peg, in the cut out, circular section of the desk, where a piece of fabric, maybe acrylic or leather, hangs to catch the filings, and you work away from you. There is a wooden ring clamp you can use, which is two pieces of wood with a hing in the middle that you shove a wedge in one side so the other side closes and can grip the wire.
Somewhere down the line I realised I was kind of trying to make burned matches without realising it. Maybe I got that from the material, like it wanted to be a burned match. Maybe from that Jeweller who I saw online yesterday. But when i realised that I started burning some matches to see what they were like.
Then it was with an electric drill/grinder thing. With different fittings designed for setting stones it allowed me to create a textured effect for the end of the matches. This was all Anna‘s idea I should add.
As you get into it your focus starts improving, your eyesight. At first you can barely focus your eyes on the head of the match you‘re working on. But soon you can see every dent and you begin to work on a minute level.
Okay then once it‘s all shaped (the main bit of the work), you buff it with an electric or with like steel wool stuff (it has a different name but I forget). I did two only with that stuff and two with the buffer and this made two matt (first two pics) and two gloss (second two pics).
Then the colouration is from sulphur. We went outside and I just dipped the match. Tada.
Glad to be in touch with material now. Obviously it complicates the concept. Or, it makes the concept a bit less interesting than the objects. I‘m not sure what‘s next. I want to try with gold. Oh yes, the economics of it are important.
I know where to get the wholesale precious metal now. And I know there are two other types of production method (at least) – sand casting and Lost Wax Casting. The former may be too intricate for small matches. The latter is like industrial and perfect and I could do as many as I wanted. So … it would be a totally different thing that what I did today. But it could mean that the vision could really easily become reality. It‘s just very very different. But there‘s something about the mass production of it that draws and repels me.
What else – oh yes, the different types of gold – with different metals in it. Another thing to consider.
I have an impulse to take my time and be apprenticed a bit before I rush ahead. But… maybe that‘s just kind of old fashioned conservatism. If I can make my concept happen maybe I should just do it. Without thinking about what people think.
But there is also something I like about working the metal again and again and again.